The semi-finished dehydrated garlic flakes after drying will go through many steps before being exported. High technology is more obvious here.
The first is to go through the color sorter, and use the color sorter to select it first, so that it is convenient to manually select. Now if there is no color sorter, it is basically impossible to work, because the efficiency is too low.
The dehydrated garlic slices after color selection are manually selected for the first and second selections. Regardless of the first selection or the second selection by hands, there are two pots, one for impurities, and the other for defective garlic slices, as shown in the picture below. As you can see above, foreign impurities are basically absent. And no matter it is the case of the first selection or the second selection, there are strong magnetic rods at the feeding port.
Although garlic slices with roots do not have such strict quality requirements as garlic slices without roots, they must be selected without foreign impurities and must go through a strong magnetic bar.
The selected garlic slices must pass through a 3X3 or 5x5 sieve before packaging to ensure the integrity of the garlic slices. Then go through the blower to remove the garlic skin, and then go through the X-ray machine and metal detector before they can be packed with confidence.
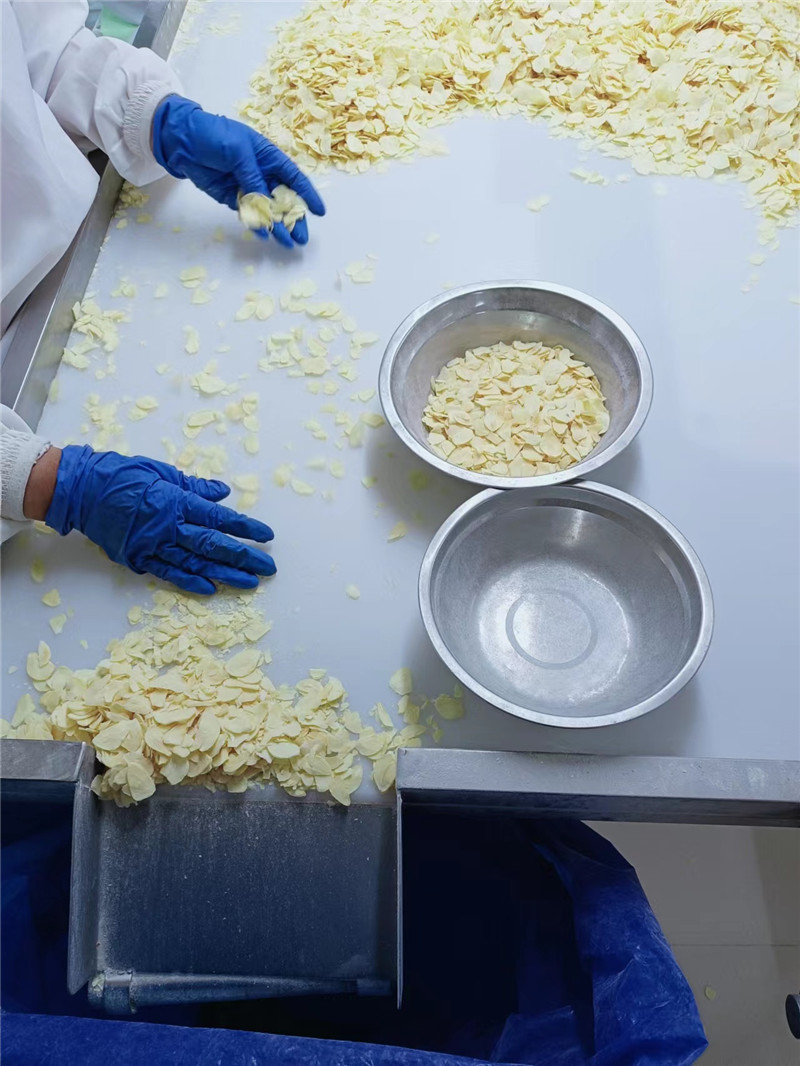
Take a look at our metal detector, isn't it very sensitive?
In order to ensure that the products will not be picked out by customers when they arrive in Japan, we use the most advanced X-ray machines and metal detectors produced in Japan. If we can't detect them, customers can't detect them, because we use the same advanced Equipment, if one day have more advanced equipment, we will definitely update it accordingly.
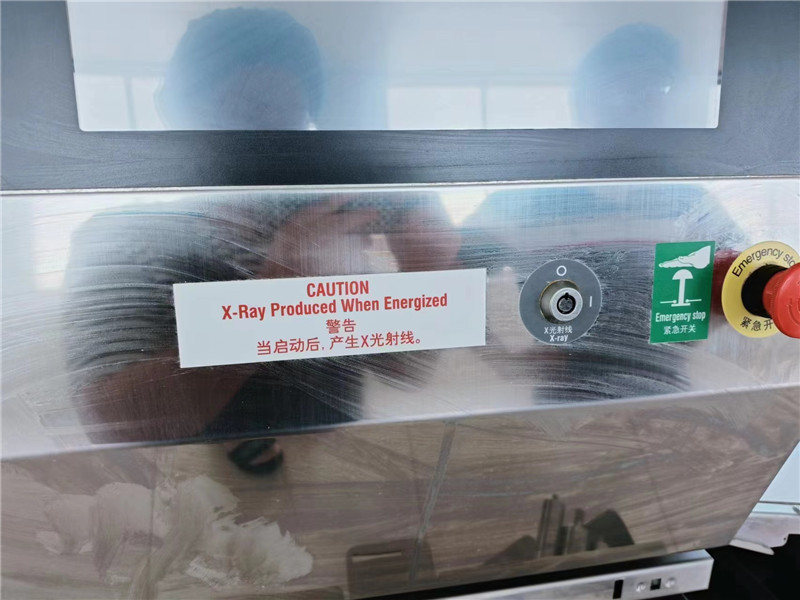
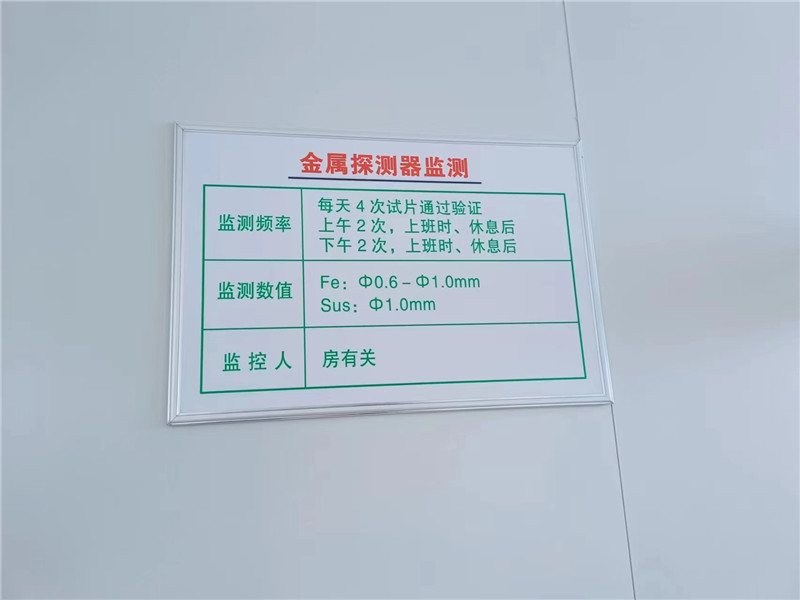
Till now, the introduction of the quality of technology-enabled products is over, and the production process of dehydrated garlic flakes is also briefly shown. A simple summary is that technology has improved quality, saved time and cost.
Post time: Jul-19-2023